Above: Nexite’s Raviv Cohen (left) with Oren Beckermus in the production floor
Caesarea, Israel based Beckermus Technologies has established a new tag production line in addition to its current Williot’s tags production line. The new line is designed to produce millions of Nexite’s smart NanoBT tags, and will begin operating on a regular basis in the coming weeks. The production line was established with an investment of more than 1.5 million dollars and is now in its final installation stage, within a building purchased by Beckermus aimed to host a dedicated production site for its customers.
Nexite was founded 4 years ago by CEO Anat Shaked and CTO Lior Shaked and has developed a hardware/software platform that enables physical products to be connected to the Cloud for advanced asset tracking and sales policy management in stores. The company has raised $100 million and employs 80 people. During a visit to the production line, hardware manager at Nexite, Raviv Cohen, told Techtime that these tags provide precise tracking capabilities that “Enables to define information-based policy management using information that was not available up until now.”
“Like a local GPS tag”
Nexite solution consists of an active tag and local reception stations that identify each tag and track its movements. The location is determined through the identification of signals transmitted by the tag (Angle of Arrival) and picked up by a number of receivers at the site, combined with an AI algorithm that provides its precise location. “It is a kind of local GPS. The local control station provides radio energy to the tag, which in turn harvests the energy and transmits standard Bluetooth signals that can be picked up by any device.”
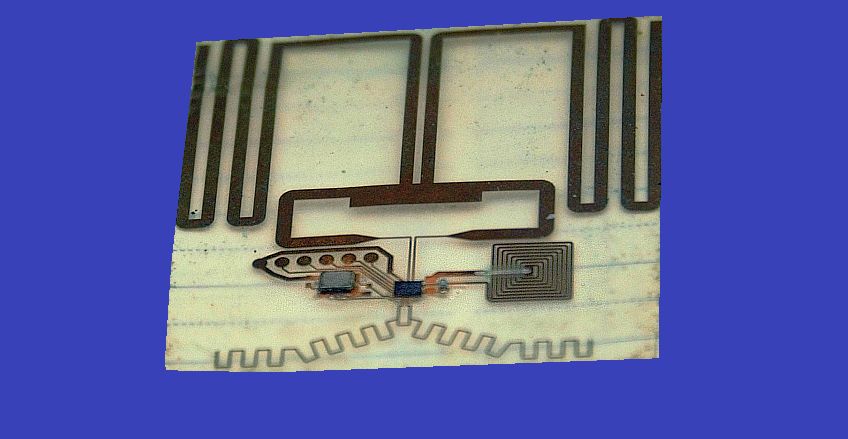
Each tag comes with unicque identification code allowing the system to collect data about the tags, identify the customer’s relationship with the product the tag is on. For example: Which products are left on the shelves, taken by customers, or measured in fitting rooms. Based on this information, Nexite provides recommendations to increase sales. Nexite started its initial sales in 2022 and has already proven the success of its recommendations. It is now ready to expand its customer base in 2023 with major Local and Global brands.
Crossing the limits of standard production
Cohen: “The tag’s price is critical to our business model. We are working in a mass market with hundreds of millions of items. Partnering with Beckermus enables us to develop a production line that suits these limitations and ensures long term production stability. Two years ago, we approached Beckermus and expressed the need for Israeli-based production line, suitable for both, serial production and development needs.”
Co-manager of Beckermus, Oded Beckermus, said that in the initial stage, the new line will produce 5,000-6,000 NanoBT tags per hour. “They consist of three different components, including a chip developed at NXP and manufactured by TSMC. Our machine providers had expressed concerns about the production complexity of the tags. So we had entered a learning process and developed a tailored production process. The machines has just arrived a few days ago and the production line is currently in its installation phase.”
Oren Beckermus (Co Manager) explained that the tailored process is based on Reel to Reel (R2R) configuration and includes 6 different machines with a total length of around 15 meters. “This is a fully automated and out-of-the-box production process: production starts with a flexible plastic reel on which the special antennas are printed. This reel is fed into a machine that contains the specialized silicone deposition wires in the desired pattern.”
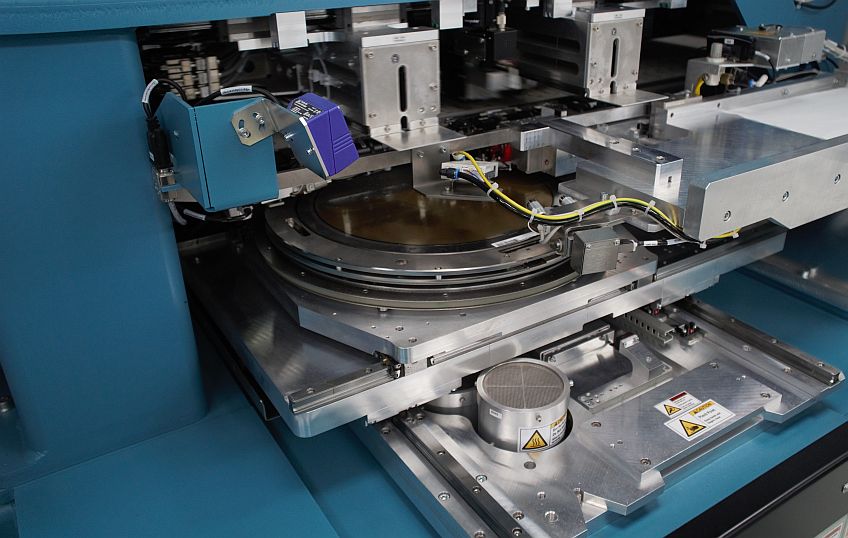
Wafer-level Production
The machine picks up each bare die from the diced wafer, according to the yield profile received from the wafer manufacturer and attaches it to the tag’s antenna. The tag then passes through the SMT machine which adds the additional SMD components. The assembly process is completed in a functional testing station that tests each tag separately to map its performance. In the final stage, an additional plastic layer is attached to protect the tag. The system is planned to enter serial production in March 2023.
How were you able to build this challenging production line?
Oren: “Ever since we established the company, we have been assembling chips. This is what we do. It is our expertise. We know how to handle wafers, assemble chips and integrate them into the final product. We employed our knowhow to tailor Muehlbauer’s production line to Nexit‘s needs. RFID production lines are usually very straight forward, however in this case we had to integrate three additional components, which was a challenge that has never been done before.”
Nexite and Beckermus had also developed a production process based on using of conductive adhesive instead of Tin soldering. This unique adhesive contains nanoparticles that provide electrical conductivity only at the pressure point – an effect that eliminates the need in soldering masks, However, it needs a precise placement of the components on the surface, with microscopic accuracy, in order to achieve electrical conductivity.
Oren: “Our collaboration with Nexite has begun after we identified the IoT as a rapidly emerging field and decided to invest in it. Since we are talking about a fully automated production process, it means we are building a competitive mass production capabilities, without relying on human labor costs.”